Share
Pin
Tweet
Send
Share
Send
It is not necessary to buy a small anvil; it can be made independently mainly from an old piece of a railway rail.

Will need
According to GOST, the face of the anvil must be made of steel grade 45L or 35L, and it must be tempered so that the hardness is within HRC 45-50. Therefore, for the manufacture of this anvil element, a strip of alloy steel with a thickness of at least 20 mm will be needed.
We will also need some tools and materials for work:
- grinder with different discs;
- grinder;
- blacksmith forge;
- welding machine;
- drilling machine;
- Oven for baking;
- blacksmith mites and pliers;
- hammer or sledgehammer;
- marker and square;
- quenching oil and tin container.
Anvil manufacturing process
We mark the anvil with the horn and tail directly on a piece of the old rail that is suitable in length and cross section.

Using a grinder and a cutting disc, we cut out the external contours of our tool, beat off the excess parts with a heavy hammer.

We continue to cut the transitional part between the top and the base of our tool, while at the same time more precisely forming the horn and tail.
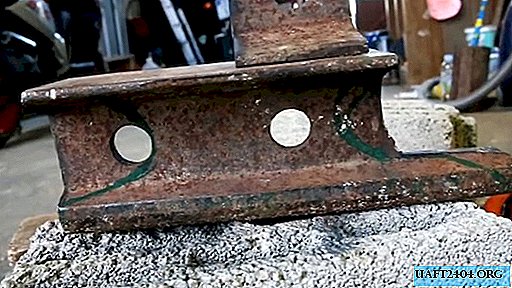

We remove rust from all accessible workpiece planes using a grinding wheel.

We give the shape of a semicircle on the grinder of the front transitional part to perceive large and constant dynamic strokes.

We sharpen the horn on a round cone, first with a grinder, and then on the grinder. On it we grind and the base of the anvil.


We mark a strip of metal with a thickness of at least 20 mm and preferably from alloy steel 45L or 35L to the size of the top of the part of the anvil from a piece of rail.

We cut out the future face of the anvil from the marked workpiece using a jigsaw and a grinder. From one edge in the plate we drill a round hole.
We grind all sides of the cut strip on the grinder and measure its size with the seat.

Pour the required amount of sunflower oil into a tin can.

We red-hot the unnecessary piece cut off from the plate in the forge and with it, heat the oil in the container. Only after that, with the help of blacksmith mites, we place it in the blacksmith's hearth and heat the plate prepared for the face of the anvil red-hot.

As soon as it acquires a crimson color, quickly and completely place it in a container with oil and hold it there until the oil ceases to boil.

Compare the hardness of the non-hardened and hardened plate with a file. An unhardened plate is easy to process, and a hardened file slides without removing a single gram of metal.
Make a vacation: put the plate in the oven and hold it there at a temperature of 200 degrees Celsius for 1 hour.


We again process the plate on all sides on the grinder and weld it to the top of the rail billet, holding clamps on both sides, first with a point, and then with a continuous seam.
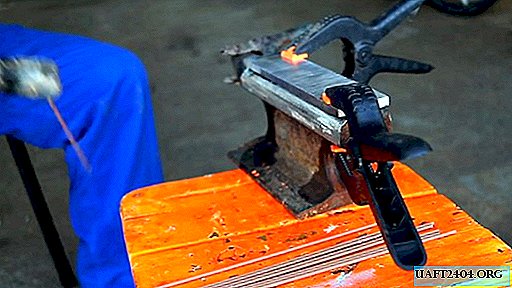

We beat off the slag with a hammer with a grinder, clean it with a grinder, weld all the shells and caverns on the face, and finally finish all the planes on the grinder.

The quality should be so high that the weld between the face and the base of the anvil is completely invisible.
Carefully choose the angle between the face of the face and the horn, first cutting, and then the grinding wheel: it must be exactly 90 degrees. Next, we subject all parts of the anvil to the same treatment.

We remove the grinding wheel from the spindle of the grinder and instead install a polishing (felt or felt) and continue the circular processing of the anvil to a mirror shine, excluding the transition section and the base.

We put the anvil on the face, mark the centers of the four holes in the corners on the base of the base, punch and run them on a drilling machine to attach the anvil to the chair, for which it is better to choose a suitable wood chock of solid wood: oak, ash, maple , birch, etc.

Homemade testing
We check the quality of our homemade anvil. We put it on the chock base down and with a hammer we begin to tap on the face over its entire surface. Everywhere a sonorous blow should be heard, and the hammer bounce off by almost the magnitude of the swing and then continue to bounce until it is completely attenuated.


Share
Pin
Tweet
Send
Share
Send