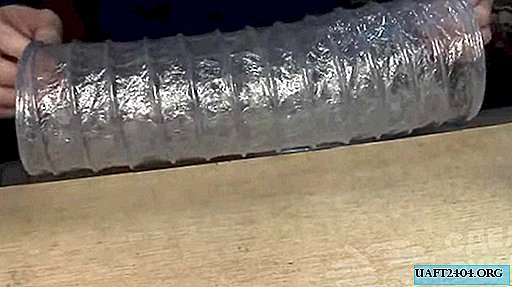
If you plan to use a table hood in the workshop or in the garage, it is very convenient to use a corrugated sleeve. You can make it yourself from an ordinary PET bottle and stretch film.
The first step is to cut the plastic bottle into strips. Moreover, it is desirable to have the bottle without constriction or level it by pumping with air and heating.
In this review, we will consider the second option. And for this you need a simple atomizer with a pump, which is screwed onto the bottle. Use it to pump air into a PET bottle.
Next, you need to twist the bottle in your hands above the gas burner. Please note that the minimum flame of a gas burner is better for leveling the bottle. But the hair dryer in this case proved to be worse.
The main stages of work
The next step is to cut the bottle into strips about 7 mm wide. How to make a simple and convenient device for cutting PET bottles is described in detail in this review.
Then the cut strips will need to be gradually heated and twisted. The main rule - first you need to twist the tape a little, and only then heat it, and as soon as the tape is twisted, you must immediately remove the finished section from the heating zone, otherwise the tube will collapse.
The collapsed area itself is less rigid, and after breaking it loses its rigidity completely.
This method is convenient in that the twisting occurs at the lowest possible temperature, the plastic does not overheat, you can immediately take it with your fingers and continue to twist.
Sleeve manufacturing process
With the help of a paper tape 3 cm wide on a plastic sewer pipe, you need to make a marking. The tape itself must be wound with a gap of 2 mm.
Further, according to the marked marking, you need to wind a spiral tube from a PET bottle. The first two turns are glued together and glued to the pipe at two points.
The spiral tube from the bottles plays the role of the inner frame, not allowing the shell of the stretch film to collapse on the bends.
It is important to pay attention to the high-quality gluing of the tubes, since the gap in the tube can no longer be eliminated and the defective piece of the sleeve cannot be cut. If there is no hot glue, then winding with a thread and impregnation with glue will help you.
Next, a stretch film in several layers is wound on a frame of plastic tubes - the first turn without tension. And the next three turns need to be wound with a stretch of 5-10%.
Stretch film is desirable to use the thinnest. The film is resistant to cuts, punctures, tears. A thin film will give greater softness in places of overlap. Next, we tighten the sleeve, leaving three turns of the tube, after which we wind the film further, and so on along the entire length of the pipe.
Useful Tips
When winding, you do not need to try to stretch the film too much and wind many layers. This will lead to the fact that the film deforms the spiral tube, from which it simply goes in a zigzag pattern.
With sufficient stretch tension, the film wraps around the spiral tube, preventing it from moving when bent. The overlap of the film during winding should be sufficient, otherwise you can tear the sleeve when pulling it from the pipe or during operation. As a rule, an overlap of three turns at a step of 3 cm is enough.
When bending, the shell between the turns folds into the sleeve, partially overlapping its cross section and increasing the resistance to air flow. Therefore, the more turns of the tube per meter of sleeve, the smaller the folds and the less the loss of resistance to air flow, which means that you can do with a weaker fan.
For details on how to make a corrugated sleeve from a PET bottle with your own hands, see this video.